Product cost is one of the most important concepts in business manageent, standing as a cornerstone for effective decision-making.
In this article, we explore what constitutes product cost and how to calculate and manage it effectively.
Key takeaways
- Product cost includes all expenses directly tied to creating and delivering goods or services, such as materials, labor, and overheads, crucial for understanding profitability and pricing strategies.
- Direct materials, direct labor, and factory overheads are the primary components of product costs, each requiring careful consideration for accurate calculation and strategic decision-making.
- Utilizing formulas to calculate product costs per unit and budgeting processes help businesses like Raymond’s Pvt. Ltd. effectively manage expenses, optimize pricing, and make informed decisions throughout the product lifecycle.
Level up your accounting with smart automation! Integrate financial data from all your sales channels in your accounting to have always accurate records ready for reporting, analysis, and taxation. See it in action with a 15-day free trial or spare a spot at our weekly public demo to have your questions answered.
Product cost: a quick look at
Product cost encompasses all the expenses directly associated with the creation and delivery of a company’s goods or services. These costs, comprising direct material, direct labor, and factory overheads, find their place in the financial statements, reflecting the investment made in producing sellable items.
Distinguishing itself from period costs—incurred for activities not directly tied to production—product costs play a pivotal role in determining product pricing. Accurate calculation of these costs is imperative for businesses to set prices that ensure profitability and prevent losses.
Types of product costs
Understanding the components of product costs is crucial for precise calculations and strategic decision-making. The three primary types are:
Direct material
Direct materials are easily identifiable and measurable raw materials directly transformed into the finished product. For instance, in automobile manufacturing, metals and plastics are direct materials, while lubricants like oil and grease fall under indirect costs.
Direct labor
Direct labor comprises the salaries, wages, and benefits paid to employees directly involved in the production process. Employees on an automobile assembly line would be considered direct labor, while administrative roles may not qualify.
Factory overheads
Factory overheads encompass indirect expenses related to production that cannot be directly traced. This category includes indirect material (e.g., glue, tape), indirect labor (e.g., supervisors, quality assurance teams), and other overheads like electricity and equipment depreciation.
Calculating product cost: steps and formulas
The equation for product cost involves summing up direct labor, direct material, and factory overheads:
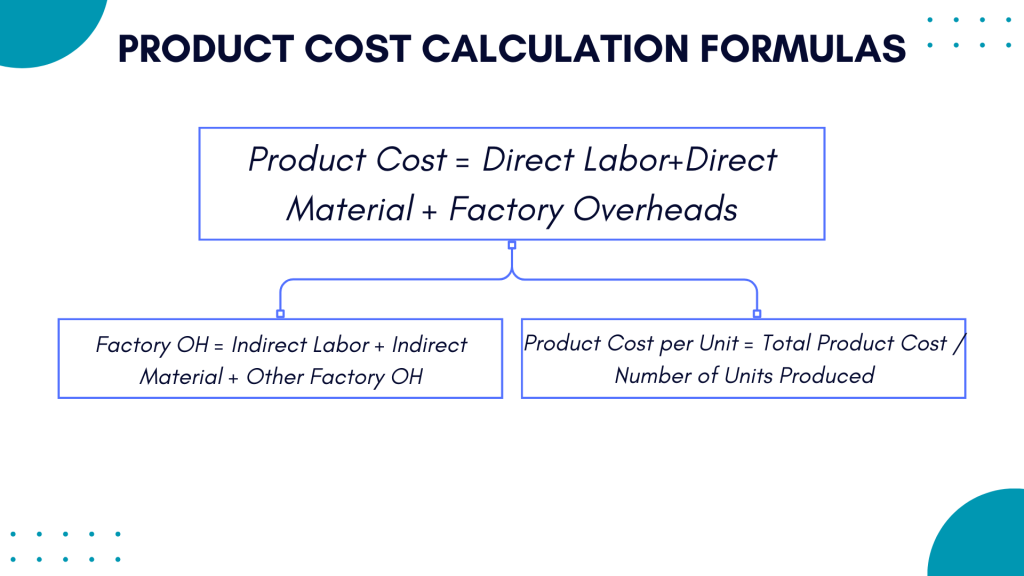
Product Cost = Direct Labor+Direct Material + Factory Overheads
Breaking down factory overheads further:
Factory OH = Indirect Labor + Indirect Material + Other Factory OH
Calculating the product cost on a per-unit basis provides a more practical perspective:
Product Cost per Unit = Total Product Cost / Number of Units Produced
Maintaining a sales price equal to or greater than the product cost per unit ensures profitability, with higher prices leading to gains and lower prices resulting in losses.
Let’s look at product costing on an example
To better understand how product costing works, let’s apply the formulas above to a real-life example. Consider a shirt manufacturing company, Raymond’s Pvt. Ltd, estimating their cost of product.
Step #1 – Direct material purchase budget
The company might start with estimating direct material costs for fabric. Calculating raw material requirements and costs using a budget helps in efficient inventory management.
Total Raw Materia l= Raw Material Required for Production + Ending Raw Material Inventory
Raw Material to be Purchased = Total Raw Material Required − Beginning Raw Material Inventory
Step #2 – Direct labor budget
Raymond’s Pvt. Ltd determines direct labor costs by estimating labor force requirements based on labor hours and units produced.
Step #3 – Factory overhead budget
Creating a budget for factory overhead costs aids in estimating variable and fixed overheads, providing insights into cash disbursement needs.
Step #4 – Overall product cost budget
Integrating direct material, direct labor, and factory overhead costs, the company calculates the total product cost, enabling the determination of the cost per unit.
Why product cost is vital for product managers
Understanding product cost is not limited to accounting departments; it’s crucial for product managers. By comprehending the costs associated with product development, managers can make informed decisions throughout the product lifecycle. This knowledge aids in pricing strategy, profitability assessment, and resource optimization.
Factors affecting product cost
Several factors influence the overall cost of developing and maintaining a software product. Considering the scope, developer costs, team structure, equipment/software purchases, other costs, and time allows product managers to make informed decisions impacting success.
Strategies to reduce product cost
Reducing product costs without compromising quality is a delicate balance. Strategies like customer research, creating a minimal viable product (MVP), analyzing tech stacks, understanding project scope, and prioritizing quality assurance can optimize costs while maintaining product standards.
Conclusion
Product cost is not merely an accounting concept. It’s a linchpin for businesses striving for profitability and sustainable growth. Whether dealing with tangible goods or software solutions, a deep understanding of product cost empowers decision-makers to set prices, allocate resources wisely, and navigate the intricate landscape of product development with confidence. In the dynamic realm of business, where every decision matters, mastering the art of managing product costs is key to unlocking success.
Continue reading: Understand comparative marketing analysis.
Want to learn more? Discover the key to effective financial management with our straightforward guide on variance reporting.
Share your thoughts
Would you like to learn more about accounting concepts? Or maybe, you would love to share some withdom with the community? Feel free to comment in the section below!