The periodic inventory system, a method used by businesses to track and manage stock levels, operates on a schedule-based approach. Unlike perpetual systems that update inventory continuously, the periodic system updates at specific intervals, typically at the end of a fiscal period. This article delves into its workings, advantages, and limitations, offering insights into its relevance in modern business practices.
What is periodic inventory?
Periodic inventory is a method of inventory management where the count and valuation of goods are conducted at specific intervals, such as monthly, quarterly, or annually, rather than continuously. This system contrasts with the perpetual inventory method, where inventory records are updated in real-time following each sale or purchase.
In the periodic inventory system, businesses determine the cost of goods sold (COGS) and update inventory levels at the end of each period. This is typically achieved through a physical count of the inventory.
Learn more about inventory system and why you need one.
This method is generally considered simpler and less expensive to implement than perpetual inventory systems, making it a popular choice for smaller businesses or those with lower transaction volumes. However, one of its main drawbacks is the lack of real-time inventory tracking, which can lead to challenges in managing stock levels effectively, especially in businesses with larger or more dynamic inventories.
When is a periodic inventory system used?
A periodic inventory system is typically used in specific scenarios where its characteristics align well with the business’s operational needs. Here are some common situations where a periodic inventory system is employed:
- Small businesses with limited inventory: Small enterprises or startups with a manageable amount of inventory often find the periodic system suitable due to its simplicity and lower costs.
- Businesses with low sales volume: Companies that do not have frequent sales transactions may opt for a periodic system as it is less cumbersome to manage with infrequent inventory updates.
- Industries with seasonal sales: Businesses that experience seasonal sales, such as holiday-specific retailers, may use periodic inventory systems to align inventory counts with the end of their peak seasons.
- Businesses with limited resources for technology: The periodic system does not require sophisticated software or technology for real-time tracking, making it a viable option for businesses with limited resources or those that prefer traditional accounting methods.
- Companies with non-perishable goods: Businesses dealing with goods that do not expire or become obsolete quickly (like clothing or hardware) might find the periodic system more practical compared to those dealing with perishable items.
- Firms conducting annual audits: Companies that prepare financial statements annually may find it convenient to align their inventory counts with their fiscal year-end for auditing purposes.
- Businesses with stable inventory levels: Companies with relatively stable and predictable inventory levels might not need the real-time tracking offered by perpetual systems and can thus opt for the periodic method.
- Organizations preferring physical counts: Some businesses prefer physical counts for accuracy or have a business model allowing periodic shutdowns (like a seasonal business) to conduct these counts.
How does the periodic inventory system work?
Periodic inventory works by updating inventory records at set intervals, such as monthly, quarterly, or annually, rather than continuously tracking each sale and purchase. Here’s a detailed breakdown of how this system operates:
Step #1. Starting with beginning inventory
The process begins with the recorded inventory level at the start of the period, known as the beginning inventory. This figure is carried over from the end of the last accounting period.
Step #2. Recording purchases
Throughout the accounting period, all purchases of inventory are recorded as they occur. However, these purchases are not immediately reflected in the inventory account. Instead, they are typically recorded in a purchases account.
Step #3. Performing a physical inventory count
At the end of the accounting period, a physical inventory count is conducted. This involves manually counting all the inventory items on hand. This process can be time-consuming and may require the business to temporarily halt operations for accurate counting.
Step #4. Calculating ending inventory
The physical count determines the ending inventory, which is the actual inventory available at the end of the period. This value is then used to update the inventory records.
Step #5. Determining the Cost of Goods Sold (COGS)
The COGS for the period is calculated using the formula:
COGS = Beginning Inventory+Purchases−Ending Inventory
This formula reflects the total inventory cost sold during the period.
Step #6. Updating the accounting records
After calculating the COGS, the accounting records are updated. The ending inventory becomes the beginning inventory for the next period.
The COGS is reported on the income statement, which affects the business’s net income for the period.
Step #7. Adjustment of the purchases account
The balance in the purchases account (reflecting the total purchases during the period) is then used to calculate the COGS and cleared out for the next accounting period.
The periodic inventory system is simpler and less expensive compared to the perpetual system, making it a suitable choice for smaller businesses or those with limited resources. However, its main limitation is the lack of real-time inventory tracking, which can lead to difficulties in managing stock levels and responding to inventory needs promptly.
Example of periodic inventory
Business profile
Business: Bella’s Boutique, a small clothing store.
Inventory system: Periodic Inventory.
Accounting period: Annual.
Starting point (January 1, 2023)
Beginning inventory: $50,000 (value of clothing in stock at the start of the year).
During the year
Purchases: Throughout the year, Bella’s Boutique purchases additional clothing inventory amounting to $80,000.
End of the year (December 31, 2023)
Physical inventory count: The store closes for a day to conduct a physical count of all the clothing items on hand.
Ending inventory: The physical count reveals an inventory value of $30,000.
Calculating the Cost of Goods Sold (COGS):
Taking the formula mentioned above, that’s what we get:
Beginning inventory + Purchases − Ending inventory = COGS
$50,000 + $80,000 − $30,000 = $100,000
COGS = $100,000.
This is the cost of the inventory that was sold during the year 2023.
Accounting updates
Beginning inventory for the next period (January 1, 2024): The ending inventory of $30,000 becomes the beginning inventory for 2024.
Income statement reporting: The COGS of $100,000 is reported on the income statement for 2023, affecting the store’s net income for the year.
In this example, Bella’s Boutique updates its inventory records only once a year. While this method is straightforward and cost-effective for a small store, it means they lack real-time data on their inventory levels, which can pose challenges for managing stock throughout the year.
Advantages of the periodic inventory system
Cost-effectiveness in setup and operation
This system typically requires minimal investment in both the setup and ongoing operations. There’s no need for expensive inventory management software or sophisticated tracking equipment, making it a cost-effective solution, especially for small businesses or startups operating on tight budgets.
Simplified accounting process
The periodic system aligns well with traditional accounting methods. It allows businesses to reconcile their inventory at the end of an accounting period with relative ease, streamlining the process of preparing financial statements.
Reduced training and technical requirements
Because it doesn’t rely on complex inventory tracking software, the periodic system reduces the need for extensive staff training and technical support. This simplicity is particularly beneficial for businesses with limited staff or those in areas with less access to advanced technology and training resources.
Flexibility in inventory count scheduling
Businesses can schedule inventory counts at times that are least disruptive to their operations. For example, a retailer might choose to conduct counts during off-peak seasons or after business hours, thereby minimizing disruption to daily sales activities.
Adaptability to various business models
The periodic system can be effectively used across a range of industries and business models, especially where inventory turnover is relatively low or where sales patterns are predictable.
Facilitates bulk purchasing decisions
Since inventory is evaluated at set intervals, businesses can make bulk purchasing decisions based on periodic reviews of stock levels, potentially capitalizing on bulk purchase discounts without the need for continuous inventory monitoring.
Clarity at fiscal year-end
The system can be particularly beneficial for financial clarity at the end of the fiscal year. Since inventory is counted and valued at specific times, it provides a clear picture of inventory levels and the cost of goods sold at crucial financial reporting periods.
Physical verification of inventory
Regular physical counts can uncover issues like theft, loss, or damage, which might not be immediately evident in more automated systems. This physical verification ensures that the actual stock matches recorded figures, highlighting any discrepancies for investigation.
Simplicity in record-keeping for tax purposes
With less frequent updates, the periodic system simplifies record-keeping, particularly when it comes to tax calculations and reporting. This can be a significant advantage for businesses without dedicated accounting departments.
While these advantages make the periodic inventory system appealing in certain scenarios, businesses need to consider their specific needs, including the size and complexity of their inventory, sales volume, and the resources available for inventory management, before choosing this system.
Disadvantages of the periodic inventory system
The periodic inventory system, while beneficial in certain contexts, also presents several disadvantages, especially when compared to more sophisticated inventory management systems like the perpetual inventory system.
Compromised decision-making ability
The lack of real-time inventory data can lead to delayed decision-making. Businesses may miss out on timely replenishment, capitalizing on trends, or responding effectively to changes in demand, potentially affecting sales and customer satisfaction.
Increased workload during inventory counts
The physical count process can be labor-intensive, requiring significant manpower and time. This is particularly challenging for businesses with large inventories or those that operate continuously, as they may need to close or disrupt operations to conduct counts.
Difficulty in managing seasonal variations
For businesses with seasonal fluctuations in inventory, the periodic system may not provide the agility needed to adjust stock levels in response to seasonal changes effectively.
Challenges in supplier relationship management
Without real-time inventory data, it can be challenging to communicate accurate inventory needs to suppliers, potentially affecting lead times and the efficiency of the supply chain.
Reduced accuracy in financial reporting
Since the cost of goods sold and inventory values are only determined at the end of the period, financial reports may not accurately reflect the business’s current financial status. This can impact the reliability of financial statements for investors, creditors, and management, emphasizing the importance of a comprehensive approach to revenue cycle management.
Inefficiency in large retail environments
In large retail operations, where inventory turnover is high, and product ranges are vast, the periodic system can be inefficient and impractical, leading to significant management challenges.
Vulnerability to theft and mismanagement
With infrequent monitoring, there’s a higher risk of theft and mismanagement going undetected. This can lead to financial losses and inventory shrinkage.
Inadequate for ecommerce businesses
For ecommerce businesses, where inventory accuracy is crucial for online order fulfillment, the periodic system’s lack of real-time tracking can result in poor customer experiences due to order delays or cancellations.
Difficulty in scaling operations
As a business grows, the limitations of the periodic inventory system become more pronounced. Scaling operations with this system can be challenging due to the increased complexity and volume of inventory.
What are the key differences between a periodic inventory system and a perpetual inventory system?
The key differences between the periodic and perpetual inventory systems are mainly in how they track and manage inventory data.
Inventory management approach
Periodic system: In this system, inventory management is more of a retrospective activity. It involves looking back over a specific period to assess inventory levels and cost of goods sold. This approach can sometimes lead to a disconnect between what’s recorded and the current state of the inventory.
Perpetual system: Inventory management is a continuous, proactive process. As each transaction is recorded in real-time, businesses can maintain a constant and accurate picture of their inventory status, allowing for immediate adjustments and decision-making.
Impact on business decision-making
Periodic system: The lack of immediate inventory data can hinder quick decision-making. Businesses may not be aware of stock shortages or surpluses until the end of the period, which can affect sales and customer satisfaction.
Perpetual system: Offers the ability to make informed decisions promptly. Real-time data supports efficient stock replenishment, pricing strategies, and sales forecasting.
Record-keeping and reporting
Periodic system: Simplifies the record-keeping process but can lead to less accuracy in financial reporting. The delay between actual inventory changes and their reflection in the books can cause discrepancies in financial statements.
Perpetual system: Provides detailed record-keeping and more accurate financial reporting. The continuous updating of inventory and COGS allows for a clearer, real-time view of the financial state of the business.
Suitability based on business scale and complexity
Periodic system: Often favored by small businesses or those with a narrow product range and lower transaction volumes. Its simplicity and lower cost make it manageable for businesses that may not have the resources or need for a more complex system.
Perpetual system: More suited for larger businesses or those with a wide range of products and high transaction volumes. Retailers, particularly those with an online presence, and businesses dealing in perishable goods often benefit from the detailed tracking it provides.
Adaptability and scalability
Periodic system: While easier to implement, it may not scale well with business growth, especially if the volume and complexity of inventory increase significantly.
Perpetual system: Highly scalable and adaptable to growing business needs. Its infrastructure can support expanding product lines and increased sales volume, making it a viable long-term solution for growing businesses.
Overall business efficiency
Periodic system: Can result in operational inefficiencies due to potential stockouts or overstocking. The need to halt operations for inventory counts can also be disruptive.
Perpetual system: Enhances overall business efficiency through better inventory control, reduced chances of stockouts, and minimized need for physical counts.
Key differences summarized
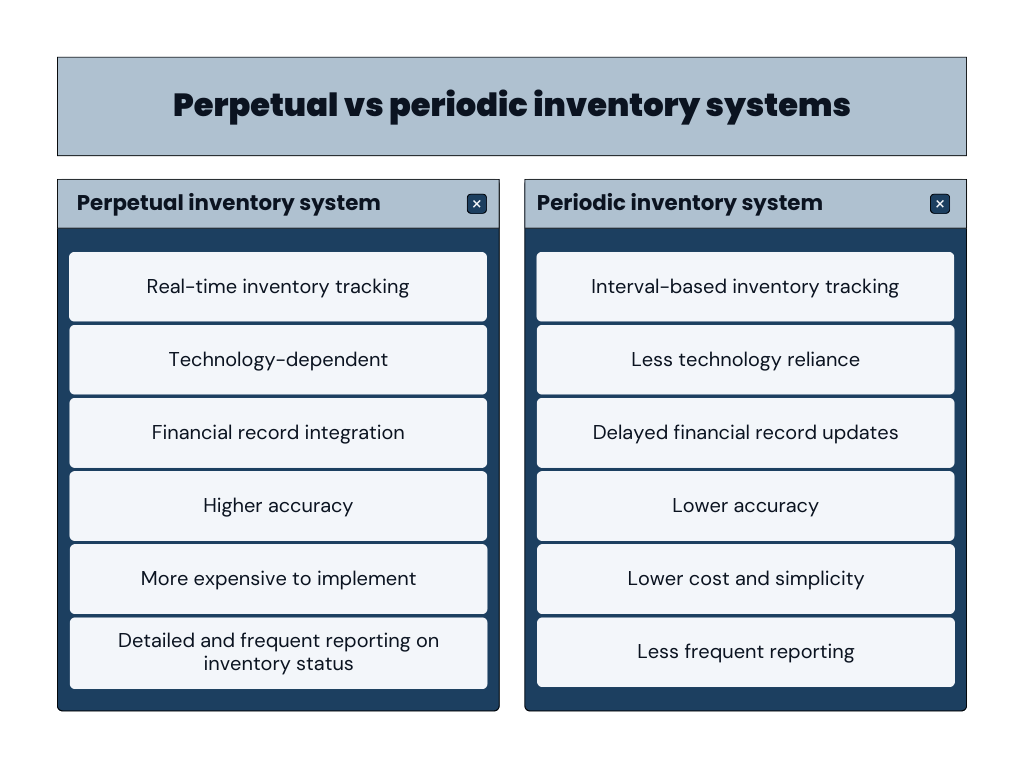
While the periodic system offers simplicity and cost-effectiveness, it comes with limitations in real-time tracking and decision-making capabilities. The perpetual system, on the other hand, provides detailed and real-time inventory management but at a higher cost and complexity. The choice between the two systems should be based on a business’s specific operational needs, resources, and long-term growth strategies.
Conclusion
In conclusion, the periodic inventory system represents a straightforward and cost-effective approach to inventory management, particularly suited to small businesses or those with limited inventories and lower transaction volumes.
While the periodic system might not match the perpetual inventory system’s detailed tracking and real-time data capabilities, it remains a viable choice for many businesses, thanks to its cost efficiency and ease of use. Its relevance endures in specific business contexts, particularly where the operational scale and complexity do not justify the need for more advanced inventory systems.
Learn more about accounting for medical practices.