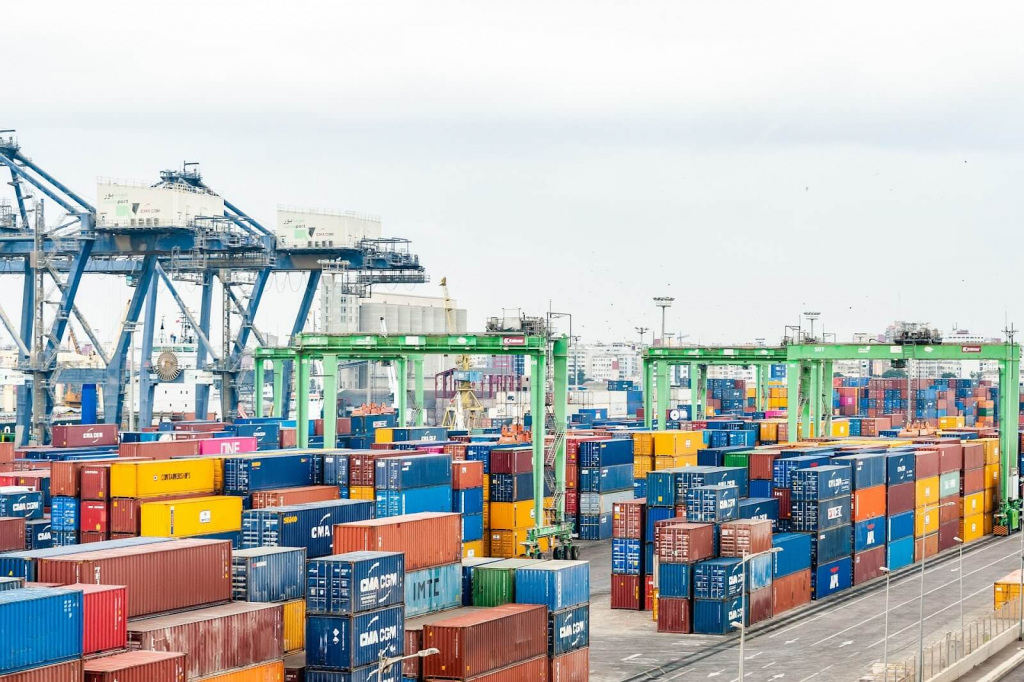
E-commerce is a vast industry that runs on several different operations that require a great deal of attention, especially if you’re a new fish in the ocean that’s the e-commerce world. One of those vital operations is fulfillment logistics.
Fulfillment logistics can be challenging, whether you’re new to the e-commerce world or not. As an entrepreneur or business manager, you’ll always need to pay attention to a lot of tasks, from inventory management and the costs of delivering, to customer service, and maintaining customer satisfaction.
Even the slightest mistake in one process can sometimes result in bad customer reviews, which is why many e-Commerce companies work with Third Party Logistic Providers who provide logistics services. There’s much more to fulfillment logistics than order delivery. Thus, in this blog, we will discuss everything you need to know about fulfillment logistics in business, including the process and benefits.
Contents:
1. What does fulfillment logistics mean?
2. Fulfillment logistics process
3. What are the benefits of fulfillment logistics for your company?
4. Challenges of fulfillment logistics in business
5. What are the different types of fulfillment logistics in business?
What does fulfillment logistics mean?
Fulfillment logistics in business involves managing the movement of products from a warehouse or distribution center to a customer or end-user. It includes all the activities related to order fulfillment, including receipt, processing, packaging, and shipping of orders.
It ensures that orders are correctly and effectively processed, picked, packed, and delivered in time for customers. People often use order fulfillment and fulfillment logistics interchangeably because they perform the same function of fulfilling customers’ orders.
Fulfillment logistics process
Fulfillment logistics is a complex process that requires careful planning, management, and execution. The process involves several stakeholders, including the customer, the enterprise, and the carrier.
Therefore, to meet your clients’ increasing needs, you must set yourself in a position to clearly understand and optimize your fulfillment logistics processes. You can do this by identifying areas for improvement and continuously monitoring and optimizing them.
The best way to become an expert in fulfillment logistics is to understand the various steps involved in the complex process. The steps involved are outlined in the points below.
Order receipt
The first step in the fulfillment logistics process is receiving the order or inventory. When the order arrives at your warehouse or distribution center, you can outsource or handle the receiving services in-house.
In any case, the incoming inventory must be counted, inspected, and inventoried by a quality control team to ensure the proper amount is received and the quality is acceptable. You could use barcodes or store-keeping units (SKUs) on your arriving products to retrieve goods from internal storage later.
Inventory storage
Inventory storage is the next step in the fulfillment logistics process. This process involves sorting and systematically storing the received inventory in a storage facility or warehouse. Inventory storage is highly vital to ensure smooth order processing. One mistake in storage can cause shipping delays, which could mean your customer doesn’t get their item on time or even at all.
Order processing
Order processing involves:
- Collection of products from storage
- Inspection of items that have been damaged
- Handing over packaging orders for companies that decide to maintain their fulfillment
It also involves checking inventory levels, verifying the order details, and preparing the order for shipment.
The importance of making sure that inventory and storage are maintained is underlined by these process steps. Order processing will be more effective when you systematically store orders.
The employees handling the inventory pickup from storage must ensure they pick the right products according to size, quantity, and color. Fortunately, many businesses have adopted the use of automated technology through the use of box-picking robots to hasten the process.
Shipping
Once the order has been processed and properly packed, the next step is to ship the orders to the customers. This involves selecting the appropriate shipping method, printing shipping labels, and arranging for the pickup of the packages.
You can use in-house riders or a third-party carrier when shipping your customer’s goods. Your 3PL will use a TMS to manage the fleet and ensure prompt delivery.
The delivery price will depend on the order destination, size, and dimensional weight. You have to understand that each carrier has its requirements for packaging and transport costs in relation to weight. To avoid delivery delays, your management team must comply with the shipping standards.
Order delivery
Finally, the order has arrived at the customer’s address. Before this occurs, you can send a shipping confirmation to the customer, so they can know when their goods will arrive. You can ask for customer feedback on the shipping and delivery process to identify any inefficiencies in the fulfillment logistics process.
Processing returns
Returns are a norm in the e-commerce industry. Many customers purchase a product with the thought of returning them later. Thus, you must have a clear return policy that will leave you dealing with the massive cost of a return.
You must process the returns and exchanges if a customer wishes to exchange an item. Inspect the returned item and send the replacements as necessary.
What are the benefits of fulfillment logistics for your company?
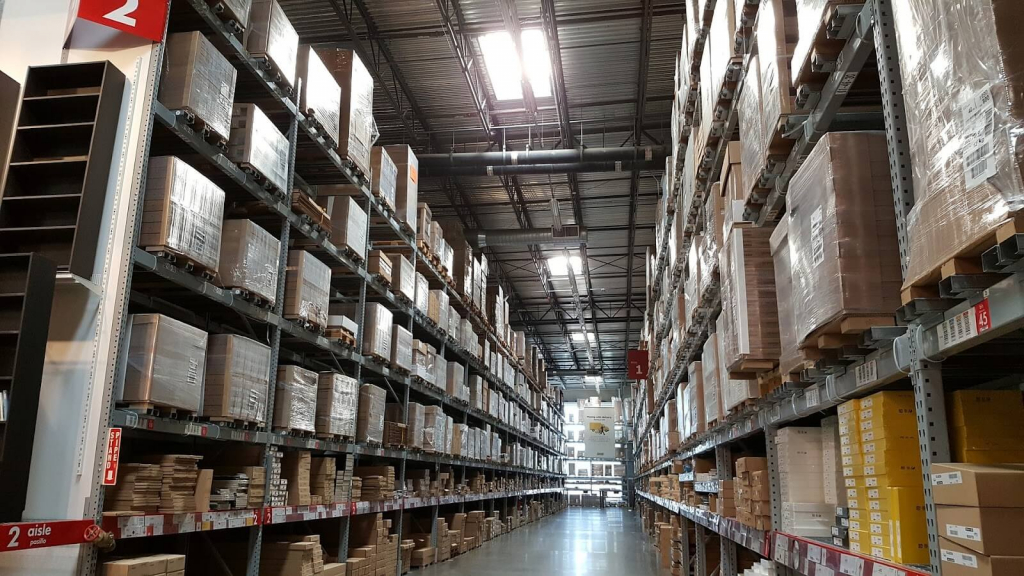
Fulfillment logistics is an essential feature of any business that sells physical products. It can bring significant benefits to the companies that have invested in them. Here are some of the benefits of having effective fulfillment logistics in your business.
Customer satisfaction
In today’s competitive business environment, customer satisfaction is vital for any business to thrive. Customers expect accurate and timely delivery of their products when they place an order. Any delay or mistake in the supply chain process can lead to customer frustration and dissatisfaction.
With fulfillment logistics, businesses can ensure that their customers receive orders in an accurate and timely manner by streamlining the order processing and delivery process. It can also build customer loyalty and trust, which may result in repeat purchases and positive word-of-mouth referrals.
Saves time and money
Outsourcing your supply-chain operations to a third-party logistics provider lets you focus on core activities, such as product development and marketing. Leaving the logistics to the experts can reduce overhead costs and improve efficiency. The logistics provider will have specialized equipment, software, and expertise for order fulfillment.
Increases flexibility
Another benefit of fulfillment logistics is increased flexibility. By working with a third-party logistics provider, businesses can scale their supply chain operations up or down to meet changing demands. This can be particularly useful for seasonal companies or businesses that experience fluctuations in demand throughout the year.
Improves inventory management
Utilizing specialized software and technology, logistics providers can track inventory levels, forecast demand, and optimize stock levels to ensure that goods are always in stock and available for delivery. This can help minimize overstocking, leading to increased costs and lost sales.
Efficient order fulfillment requires accurate inventory management, which involves keeping track of stock levels, replenishing inventory, and forecasting demand. Poor inventory management can lead to stockouts, excess inventory, or mismanaged orders, resulting in delays and errors in order fulfillment. These issues can also result in additional costs, such as rush shipping or lost sales due to stockouts. Effective inventory management is essential for smooth order fulfillment and can help businesses save money, time, and resources.
Boost cash flow management
Fulfillment logistics also impacts cash flow management. Inefficient order fulfillment processes can delay invoicing, payment processing, and other financial operations. This can result in delayed payments and cash flow problems, impacting the business’s financial stability. Accurate and timely order fulfillment can help businesses streamline their invoicing and payment processes, improving cash flow management and reducing the risk of financial issues.
Aids expansion
Fulfillment logistics is essential for businesses looking to expand their operations. You need to handle increased order volume and complexity effectively as your business grows. Inefficient order fulfillment processes can lead to delays, limiting the business’s ability to scale. On the other hand, efficient order fulfillment processes can help businesses scale their operations and meet increasing demand.
Access to new markets
By partnering with an international third-party logistics company, businesses can make it easier and more effective for customers worldwide to receive their products. In addition to increasing revenue and sales, it can also contribute to establishing a presence in new markets.
Challenges of fulfillment logistics in business
Implementing an optimized fulfillment strategy for shipping products is even more critical to avoid common fulfillment issues, given supply chain challenges over the last few years. Let’s discuss some challenges in implementing efficient fulfillment logistics and how your business can overcome them.
Inventory management
Managing your inventory is one of the biggest challenges you’ll face when implementing fulfillment logistics. It is essential to have a good inventory management strategy to ensure your business has the right products available when customers need them.
However, inventory management can be daunting, especially if you’re a company that deals with large volumes of products. Keeping track of stock levels, reordering products, and maintaining adequate inventory levels can be time-consuming and challenging.
Warehouse staff will waste time searching for inventories, delaying shipments and deliveries to the customer when there is poor inventory control. This is why you must develop efficient inventory management systems that help to monitor stock levels accurately, reorder products promptly, and prevent stockouts.
Forecasting demand
Customer demand changes with economic conditions, seasons, and news cycles. Overestimating customer demand will leave you with an obsolete inventory in your warehouse that takes up valuable storage space. A space that beneficial products could occupy. To avoid this, you could implement a Just In Time (JIT) inventory system where you only order or receive products as they are needed.
However, underestimating demand means your company will have long delays due to backorders. Due to this, many customers will look for another dealer to fulfill their purchase. To avoid this, you can maintain your safety stock. Safety stock is extra inventory you keep on hand to ensure you can fulfill orders even during unexpected spikes in demand. Maintaining a sufficient safety stock means you can reduce backorders because you have a buffer to handle unforeseen demand fluctuations.
Delivery efficiency and tracking
Your customers’ trust in you and the assurance that they will receive their product improves when you provide them with an approximate date for shipment, tracking number, or notification of delivery during the transportation process.
Also, order tracking allows you to have a greater degree of control over the supply chain process. In the future, you’ll be able to see exactly where the bottlenecks are and fix them. Order tracking is the best way to gain happy customers and keep them returning.
What are the different types of fulfillment logistics in business?
Fulfillment logistics is a subset of the larger supply chain process, and there are different models you can choose from to help your company.
In-house fulfillment
As the name suggests, in-house fulfillment involves using your employees for fulfillment services. Everything involved in the fulfillment process will be handled by your staff, including storage and product shipment from the company’s storage facility.
In-house fulfillment is best for established companies that have a vast amount of labor force and prefer to have more control over the whole fulfillment process.
Third-party fulfillment
This is the most popular category of fulfillment logistics because it saves companies much time, energy, and money. The whole fulfillment process is handled by an order fulfillment or a third-party logistics (3PL) company, from inventory receipt from the manufacturers, to delivery of the products to the customer.
Mixed fulfillment
Mixed or hybrid fulfillment involves dropshipping and doing in-house fulfillment logistics. For example, a company may process certain orders in-house, such as custom items or items that have to be assembled before shipping, while also using drop shipping services for non-custom items. This model of order fulfillment is ideal for companies that are undergoing rapid expansion or want more flexibility.
Dropshipping
Dropshipping is the same as outsourcing, but there is no inventory to keep track of. The retailer does not keep the goods that it sells in stock. Instead, the retailer buys these products from a third-party supplier when they are sold.
This supplier can be a manufacturer or business that buys products from manufacturers for the purpose of selling to dropshippers. All orders are taken care of by the supplier and delivered to your customers. You are only charged for the sale of your products.
Conclusion
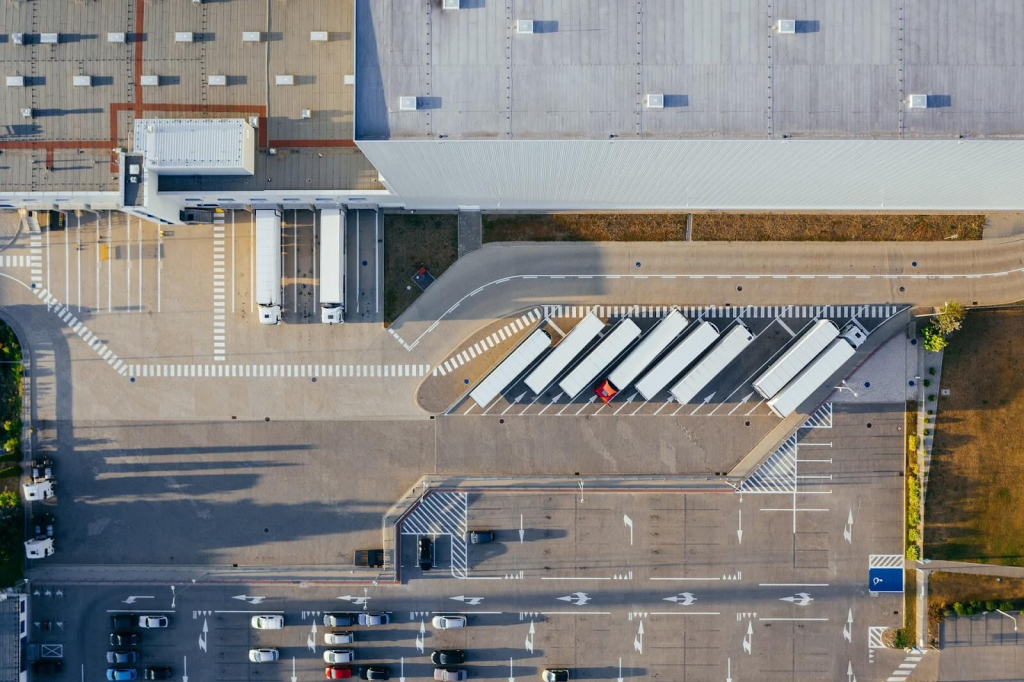
The e-commerce business journey to a happy, repeat customer base begins with the design, manufacture, and marketing of your product. A huge factor in the satisfaction of customers, which can create or destroy a company, is that you package your product and ship it on time.
If your business is growing, you will face challenges with managing fulfillment logistics, or you will meet them after your business scales up. Organizing operations such as inventory stocking, timely packing, delivery, or processing returns will likely be more challenging. Most of the time, this begins with something basic like needing more space to store your goods. Without adequate storage space, all your other operations will crash because of the domino effect.
Demand for faster and more convenient deliveries is continuously increasing, so you have to utilize an efficient third-party logistic company to provide adequate fulfillment services. We hope this article will help you make the right choice if you’re on the verge of deciding what to do about your fulfillment logistics.
It’s interesting to learn what could be a challenge when shipping and delivering your products. Not long ago, my cousin mentioned he’d like to expand his operations by adding nationwide delivery services. My cousin will benefit from reading about fulfillment logistics that use accurate tracking systems.
I am so glad you found this topic helpful!
This blog masterfully delves into the intricate world of fulfillment logistics. The emphasis on its critical role in business success is on point. The step-by-step breakdown of the fulfillment process is informative and makes it accessible to all. It serves as a valuable resource for businesses aiming to streamline their logistics operations.
Thank you! I’m very happy you liked it!
Steel containers are standardized, stackable, and versatile, making them an integral part of modern logistics and warehousing operations.
Very informative blog, benefits and challenges are really means a lot in an logistics business.
Many steel containers are equipped with tracking technology, enabling real-time monitoring of the location and condition of goods in transit.