Every product tells a story–not just of design and delivery but of the costs and decisions that bring it to life. For businesses, understanding the cost of goods manufactured (COGM) isn’t just about crunching numbers; it’s about uncovering the real drivers behind profitability and efficiency. From tracking production expenses to setting competitive prices, COGM holds the key to staying in control of your operations.
If you want to optimize your production process, mastering COGM equips you with the insights needed to stay ahead. So, let’s break it down step by step, uncover the formulas, and dive into examples that make it all crystal clear.
What is COGM?
Cost of goods manufactured (COGM) reveals a business’s total cost to make finished products. It includes everything tied to production–raw materials, labor, and factory overhead–and takes center stage on the income statement.
Unlike general expenses such as utilities or marketing, COGM sticks strictly to manufacturing costs. While it’s closely related to total manufacturing cost (TMC), COGM only focuses on completed goods, leaving unfinished items to be tracked as ending work-in-process (WIP) inventory.
Why is COGM important?
Cost of goods manufactured (COGM) is important for manufacturing businesses because it helps to:
- Track production costs: COGM breaks down all costs–materials, labor, and overhead–so you know exactly where your money goes.
- Set prices: It helps set competitive prices that cover costs and lock in strong profit margins.
- Improve efficiency: It’s essential for calculating the cost of goods sold (COGS) and keeping financial reports spot-on.
- Support financial reports: Regular COGM checks highlight where to cut costs, improve processes, and stay ahead.
In short, COGM is your go-to tool for controlling costs, maximizing profits, and running a lean, efficient operation.
COGM vs. COGS: What’s the difference?
While the cost of goods manufactured (COGM) and cost of goods sold (COGS) might sound similar, they serve different purposes in understanding your production and sales costs. Now you know what COGM is, but what about COGS, and how is it different from COGM? Let’s find out.
What is the cost of goods sold (COGM)?
COGS zooms in on what it costs to produce the goods you’ve actually sold during the period. It builds off COGM but includes adjustments for finished foods inventory at the start and end of the period.
COGS is what you see on your income statement and directly impacts your gross profit. |
Key differences
Key differences | COGM | COGS |
Scope | Focuses on production costs for finished goods | Focuses on costs for goods that have been sold |
Inventory | Includes work-in-process (WIP) inventory | Includes adjustments for finished goods inventory |
Purpose | Helps evaluate production efficiency | Shows how much it costs to generate revenue |
The big picture
- COGM shows you the total cost of manufacturing products.
- COGS narrows it down to what you spent on the goods that were sold.
In short: COGM is about making it, and COGS is about selling it. Both are key to understanding your manufacturing and sales performance. |
The cost of goods manufactured formula
Calculating COGM means adding up all the direct and indirect costs involved in making products, plus accounting for changes in work-in-process (WIP) inventory. To figure out COGM, you need to know the total manufacturing costs (TMC) and the WIP inventory values at the start and end of the period.
Here’s the COGM formula:
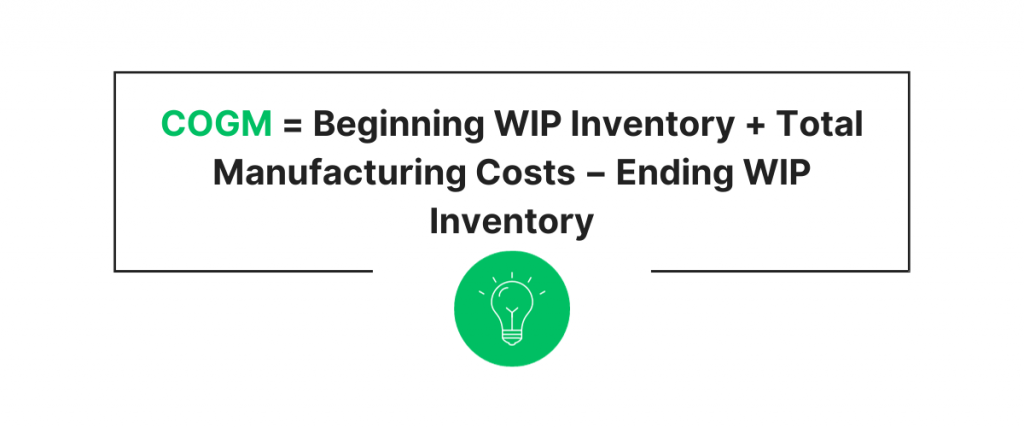
Let’s take a closer look at the key components of the cost of goods manufactured formula:
Total manufacturing cost (TMC)
Total manufacturing cost (TMC), also called total cost of production, is the all-in number for what it takes to make goods during a specific period. It covers everything tied to production–raw materials, labor, and factory overhead.
What makes TMC different from COGM? TMC skips over changes in work-in-process (WIP) inventory, while COGM includes them.
What’s in TMC?
- Direct materials: The cost of raw stuff that becomes your product.
- Direct labor: Wages paid to workers directly involved in production.
- Manufacturing overhead: The behind-the-scenes costs associated with the production like utilities, equipment upkeep, and depreciation.
In a nutshell, TMC isn’t just a number–it’s a tool. It shows where your money’s going, helps you price smarter, and points out where you can cut back.
Work-in-process (WIP) inventory
Work-in-process (WIP) inventory is a big piece of the cost of goods manufactured (COGM) puzzle. Listed as a current asset on the balance sheet, WIP represents the cost of products still in production, including materials, labor, and overhead.
WIP gets calculated at the end of each accounting period. The beginning WIP is what’s left unfinished from the previous period, while the ending WIP is what’s still in progress after finished goods are accounted for. Most manufacturers aim to keep ending WIP low–it frees up cash, cuts taxes, and makes accounting a whole lot easier.
Note: If WIP is zero, TMC equals COGM. But calculating WIP can get tricky, with overhead and taxes needing to be factored into every unfinished product. |
How to calculate the cost of goods manufactured?
Let’s break down how to calculate cost of goods manufactured step by step, using real-world examples to make it simple and actionable.
Step 1: Gather key data
Before you dive in, collect these essentials:
Work-in-process (WIP) inventory:
- Beginning WIP inventory: The value of unfinished goods at the start of the period (e.g., $5,000).
- Ending WIP inventory: The value of unfinished goods at the end of the period (e.g., $3,000).
Direct costs:
- Direct materials used: The raw materials that go into production. Calculate like this:
Direct materials used = beginning raw materials inventory(e.g., $4,000) + raw materials (e.g., $8,000) – ending raw materials inventory(e.g., $2,000) Direct materials used = 4,000 + 8,000 − 2,000 = 10,000 |
- Direct labor: The wages paid to workers directly building your products (e.g., $12,000).
Indirect costs:
- Manufacturing overhead: Expenses like utilities, factory maintenance, and equipment depreciation (e.g., $6,000).
Step 2: Calculate total manufacturing costs (TMC)
Add up all the production costs from the period:
TMC = Direct Materials Used + Direct Labor + Manufacturing Overhead TMC = 10,000(Materials) + 12,000(Labor) + 6,000(Overhead) = 28,000 |
Step 3: Plug it into the COGM formula
Now it’s time to complete the COGM calculation:
COGM = Beginning WIP Inventory + TMC − Ending WIP Inventory COGM = 5,000(Beginning WIP) + 28,000(TMC) − 3,000(Ending WIP) = 30,000 |
Step 4: Understand the Result
The COGM of $30,000 represents the total cost of goods completed and ready to sell during the period. This is key for calculating your cost of goods sold (COGS) and analyzing your production efficiency.
Quick recap example
Here’s a quick summary of the numbers:
- Direct materials used: $10,000;
- Direct labor: $12,000;
- Manufacturing overhead: $6,000;
- TMC: $28,000;
- Beginning WIP: $5,000;
- Ending WIP: $3,000;
- COGM: $30,000.
COGM vs. COGS calculation
Data for the quarter:
- Beginning WIP inventory: $10,000;
- Ending WIP inventory: $8,000;
- Direct materials: $50,000;
- Direct labor: $30,000;
- Manufacturing overhead: $20,000;
- Beginning finished goods inventory: $15,000;
- Ending finished goods inventory: $10,000.
COGM calculation:
COGM = Beginning WIP + Total Manufacturing Costs − Ending WIP COGM = 10,000 + (50,000 + 30,000 + 20,000) − 8,000 = 102,000 |
COGS calculation:
COGS = Beginning Finished Goods + COGM − Ending Finished Goods COGS = 15,000 + 102,000 − 10,000 = 107,000 |
Now you know what COGM and COGS are. But if the COGM calculation is clear, what about COGS? How do you calculate it and meet all the requirements? Automation is definitely the way to go.
How can Synder simplify accounting?
Selling your products across multiple platforms? Managing financial data can quickly become overwhelming, especially when calculating your cost of goods sold (COGS). That’s where accounting tools like Synder come in.
Synder streamlines the process by automating financial data from all your sales channels, ensuring accurate COGS calculations. This allows you to set competitive prices, maintain healthy profit margins, and keep your finances organized effortlessly.
Why Synder? Let’s see what features Synder offers to tackle this question:
1. Real-time data syncing
Synder automatically syncs your financial data—sales, fees, refunds, and more—as transactions happen. Whether it’s Shopify or PayPal, Synder updates your accounting software instantly, giving you a clear view of your cash flow.
2. Automated COGS tracking
Synder matches products by name or SKU, updates quantities, and adjusts COGS accounts. Got new products? Synder creates them and assigns them to the right account—no duplicates, no headaches.
3. Smart product mapping
Different product names across platforms? No problem. Synder’s product mapping feature matches and tracks items seamlessly, even if you have different product names across platforms, you can still track them as one product. Consistency has never been easier to achieve.
4. Automated categorization
Every business is different. And with customizable rules, you can categorize transactions your way. Synder puts you in charge by letting you customize rules for recording different types of transactions and deciding how and when your data syncs.
5. Error-free reconciliation
Synder accurately matches transactions recorded in your accounting software with corresponding bank deposits and expenses. This ensures every dollar is recorded accurately, making reconciliation fast and stress-free.
Ready to let Synder do the heavy lifting? Join our Weekly Public Demo to discover how Synder can revolutionize your accounting workflow or try our 15-day free trial to test its features yourself.
Conclusion
The cost of goods manufactured (COGM) isn’t just a number–it’s the heartbeat of your production process. It reveals how efficiently your business operates, uncovers opportunities to cut costs, and empowers you to make data-driven decisions that fuel growth.
Mastering COGM goes beyond improving your bottom line–it’s about building a smarter, more resilient business. By understanding the true costs behind your production, you can refine processes, adapt to challenges, and seize opportunities with confidence. For manufacturers aiming to thrive in a competitive landscape, COGM is more than a metric–it’s a roadmap to sustainable success. d maintain a competitive edge.